达涅利Energiron工艺方案:让低碳排放炼钢成为可能!



采用ENERGIRON专利技术实现直接还原。

以氢气为还原剂的直接还原铁生产是一种技术成熟的“绿色”炼钢解决方案,其具有优化电力成本的潜力。
钢铁在我们的生活中无处不在,是现代社会可持续发展的核心。钢铁行业是全球循环经济不可或缺的一环,因此也是实现成功交付和维护可持续未来的一部分。
钢铁是真正的“绿色”材料,可无限循环利用,其副产品和余能也是宝贵的资源。
然而,如今钢铁行业的二氧化碳排放量占全球的7%,在过去十年中,每生产一吨钢,就会排放1.83吨二氧化碳。
世界要想可持续发展,就需要大量的钢铁。由于发达经济体对钢铁的需求如此之大,而世界上约四分之三的地区仍处于发展阶段,因此需求预测表明,到2050年,钢铁年消费量将在26亿吨左右。尽管有回收或再利用现有库存,但仍必须解决对环境的影响(图1)。

现有技术为设备提供了非常高的能源效率,因此为了与《巴黎协定》的目标保持一致,即全球平均气温较前工业化时期上升幅度控制在两摄氏度以内,并朝着减少二氧化碳排放的方向迈进一步,在初级炼钢中需要彻底改变生产模式。
欧盟委员会的发展蓝图要求到2050年,欧洲工业的二氧化碳排放量要比1990年减少80%至95%,目前欧洲的二氧化碳排放量税率为25欧元/吨,未来几年将会稳步增长,这将影响所有设备的整体运营成本和竞争力。
其中一种可行性减排方案,理论上可以在2010年至2050年间使每吨钢的排放量减少60%,这取决于利用炉顶气回收技术对现有高炉进行改造的效果,并在欧洲全面部署碳捕获和储存(CCS)。然而,这项技术在工业规模中的可行性尚未被验证。此外,到目前为止,CCS在欧洲的经济可行性和普遍适用性似乎存在问题。由于越来越多的成员国抵制CCS,并且也缺乏相关商业案例,该技术在可预见的未来内能否被整个欧洲所接纳尚未可知。
尽管如此,目前也还有一种成熟且经过工业验证的解决方案可以将初级冶炼生产中的二氧化碳排放量即刻减少50%:基于气体的直接还原。
达涅利正在积极推动从传统高炉(BF)-氧气顶吹转炉(BOF)向更灵活、更环保的直接还原(DR)-电弧炉(EAF)转变,并向市场推出由特诺恩和达涅利共同开发的Energiron专利技术。
由于其先进的设计,Energiron将是唯一的一种能够使每种补给气体均保持标准工艺配置的技术,从而可确保操作人员完成多功能操作。事实上,Energiron的设计不仅可使用天然气,还可使用气体还原剂,如焦炉煤气(COG)、高炉煤气、氢气或由煤气化或外部转化炉产生的合成气。
因此,Energiron是从BF/BOF转向DRP/EAF(图3)的完美过渡技术。例如,在第一步时可使用COG或NG作为还原气体,并在高炉中使用产生的DRI。这样就可以在保持现有BF/BOF设备的所有下游配置的同时减少二氧化碳排放。
第二步,可以安装一个电弧炉并考虑向其连续输送(超过600℃的)高温直接还原铁,节约150千瓦时/吨的直接还原铁,从而最大限度地提高效率并减少排放。
最后也就是在第三步中,可以通过拆除BF/BOF并增加DRP/EAF设备的容量来完成整个过渡。
这可能只是一种过渡情况,其中可使用Energiron专利技术(图2)。

氢气:直接避免碳排放(CDA)解决方案
Energiron工艺方案最初是为了使用氢气而设计的,这是朝着绿色和循环经济迈出的一步。因此,它非常适合以可持续的方式生产钢材。使用氢气是减少温室气体排放的最终答案,因为氧化铁还原的唯一副产品是水:Fe2O3 + 3H2—> 2Fe + 3H2O!
氢气将消除钢铁生产过程中的碳足迹,从而直接避免了碳的排放(CDA)。(见图3)

很明显,生产无碳氢气的唯一方法是以水电解为基础,利用可再生能源提供所需的电力。(见图4)
对于无碳氢能发电,有不同的可用电解槽技术,如质子交换膜(PEM);对于常压碱性电解槽(AAE),其设备已用于生产高纯度氢气,功耗在3.8至4.6 kW/Nm3之间;对于高温电解槽(HTE),其规模目前较小,需使用蒸汽,相关功耗约为3.6 kW/Nm3。根据替代燃料的可用性,较大的PEM和AAE模块目前在氢气的4000 Nm3范围内,这足以运行一个DRI约为40000-50000t/a的DR模块。
对于较大的DR设备规模,将按比例复制可用模块。
在欧洲,以氢气为目标的项目开始出现:总的来说,欧洲正引领着集中使用氢气炼钢的潮流。以此为目标的项目包括:
- 蒂森克虏伯钢铁公司(ThyssenKrupp Steel)的Carbon2Chem®项目旨在利用钢铁厂排放的二氧化碳和可再生能源的余能进行化学生产,目前正转向CDA方法。
- 奥钢联、西门子和Verbund正在林茨为H2 Future项目建一个“绿色H2”试点工厂。
- SSAB、LKAB和Vattenfall共同投资了HYBRIT项目,旨在使用氢进行钢铁生产。Energiron正在提供设备和技术支持。
- 萨尔茨吉特公司对高碳DRI进行了SALCOS研究,将其作为(终将取代高炉/氧气顶吹转炉的)高炉和电弧炉的原料,并实施了GrInHy项目,通过利用可再生能源的可逆高温电解槽产生氢气。萨尔茨吉特公司选择将Energiron作为绿色钢铁转型的最佳可用技术(BAT)。
- 在荷兰,也有一些重要的项目为当地的冶金工业提供氢气。
氢气炼钢的经济效益
在运营成本方面,水电解制氢意味着直接与电网成本挂钩。就4.5 kWh/Nm3左右的氢气而言,基于Energiron ZR技术的DRI能耗约为2.5 MWh/t。由于绿色氢气将由可再生能源生产,因此需要对其电力成本进行分析。问题的关键是,氢能发电能耗较高,导致能源成本也很高。
例如,目前在德国,可再生能源的发电成本已降至0.05欧元/千瓦以下,这就意味着直接还原铁生产所需的天然气成本约为13欧元/GJ,仍然很高。但是与补水、电解模块资本支出、氢气储存和运输(如适用)和二氧化碳排放目标相关的成本以及相应的信贷,也应计入成本等式。
据国际可再生能源机构(IRENA)称,可再生能源发电的成本很快将普遍低于化石燃料发电。
到2020年,目前所有投入商业使用的发电技术都将归入化石燃料燃烧的成本范围内,其中大部分都处于较低水平,甚至会低于化石燃料。
2016年和2017年,迪拜、墨西哥、秘鲁、智利、阿布扎比和沙特阿拉伯的太阳能光伏(PV)能源拍卖价格创历史新低。这表明只要条件合适,就有可能实现0.03美元/千瓦时的均化发电成本(LCOE)。据IRENA称,新建陆上风电场的加权平均电力成本可低至0.03美元/千瓦时。
为了在基于绿色H2的直接还原铁生产方案中赢得竞争力,根据当前的电解槽效率,在无二氧化碳排放量的情况下,可再生能源的电力应为<0.02美元/千瓦时。资本支出也必须大幅削减。在未来几年内即有望实现(表1)。

因此,很容易理解在使用还原性气体补给方面具有最高能效和灵活性的设备是多么重要。通过使用100%的氢气,Energiron工厂可以达到低至2.0 Gcal/tDRI的消耗值,这一非凡的结果使其成为未来的技术。
结论
即使在当前这样充满挑战的金融时代,也需要对新技术进行重大投资。
尽管大幅降低钢铁生产碳足迹的技术已经成熟,但要想与《巴黎协定》规定的规模和速度相适应,就必须依靠大量的长期投资以及行业和机构之间的合作。
由于约30%的钢铁贸易为国际贸易,因此相关政策还必须营造一个公平的竞争环境,以确保一个地区的钢铁企业在与其它地区的钢铁企业的竞争中不会处于劣势。
同时,对于低碳足迹、绿色钢铁生产,目前有一个在技术上行之有效的解决方案:使用高达100%氢气的Energiron ZR工艺。
高效电解槽中(由可再生能源提供动力)的“绿色”氢气是一种无碳炼钢方式,但前提是要保证未来电力成本和投资的最优化。

来源:达涅利零距离
免责声明:本公众号所载文章为本公众号原创或根据网络搜集编辑整理,文章版权归原作者所有。转载请注明来源;文章内容如有偏颇,敬请各位指正;如标错来源,请跟我们联系!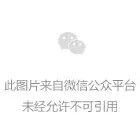
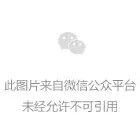
最新评论
推荐文章
作者最新文章
你可能感兴趣的文章
Copyright Disclaimer: The copyright of contents (including texts, images, videos and audios) posted above belong to the User who shared or the third-party website which the User shared from. If you found your copyright have been infringed, please send a DMCA takedown notice to [email protected]. For more detail of the source, please click on the button "Read Original Post" below. For other communications, please send to [email protected].
版权声明:以上内容为用户推荐收藏至CareerEngine平台,其内容(含文字、图片、视频、音频等)及知识版权均属用户或用户转发自的第三方网站,如涉嫌侵权,请通知[email protected]进行信息删除。如需查看信息来源,请点击“查看原文”。如需洽谈其它事宜,请联系[email protected]。
版权声明:以上内容为用户推荐收藏至CareerEngine平台,其内容(含文字、图片、视频、音频等)及知识版权均属用户或用户转发自的第三方网站,如涉嫌侵权,请通知[email protected]进行信息删除。如需查看信息来源,请点击“查看原文”。如需洽谈其它事宜,请联系[email protected]。