造车,到底有多难?

造车,到底能有多难?这个问题真的是极难回答。

按照目前多家汽车制造商给出的数据,一辆成品轿车所包含的总部件数量大约在5万个,这些零部件种类繁杂。这也意味着想要将这些零部件全部生产出来,对生产设备、人工、物料、资金需求即便用“庞大”来形容,可能都差点意思。
简要一点说,在汽车产品和工业体系高度发达的当下,造车的难度不再仅仅是一家厂商的事,而是你怎么样能够“融合”到产业中的问题。
我们不妨来参考另外一组数据:2017年,华晨宝马成功将接近39万辆汽车交到了用户手中,同期,还向中国本地359家零件采购商支出了267亿人民币,用以零配件采购。
听起来数字就已经不小,但实际中这还不只是那种“给钱就能解决”的问题。究竟汽车工业的水有多深?8月底,虎嗅就跟随华晨宝马,到他们自己的生产基地以及数个国内重要供应商中参观了一番。
多地参观采访下来的感受再直接不过:造车不易,造高端车更不易。
打造基础供应链,造车绕不过的一道“坎”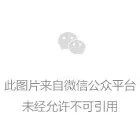
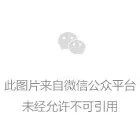
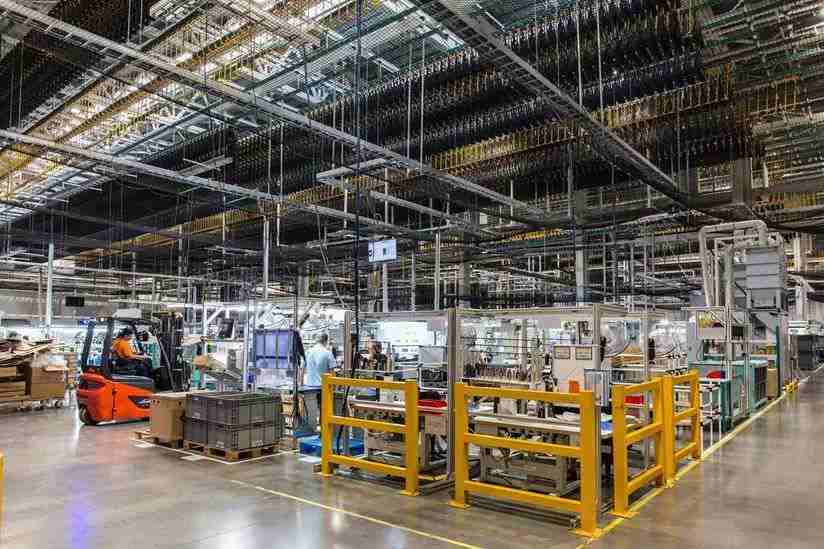
德科斯米尔先进的天体库系统(零件直接悬挂在生产线之上)
我们先说说为什么一定要依赖供应链的力量。
一辆车中大大小小5万多个零件,单原料种类就各式各样,有金属、有塑料、有皮草、有布料、有线材,多种多样的材料也给不同的零件带来完全不同的生产工艺。这也让这些零件的生产过程各不相同,由此导致生产线的配置、工序的设定等一系列细节也完全不同。
参考开篇的数字,只靠车厂自己,就是要自己一个人干完几百家供应商的活,然后打造至少上千条生产线,养上至少数万名员工,产业规模千亿可能都不止。这么大的“白日梦”,只会让人噎死。
真正明智的办法,是将其中很多的零部件“交”给供应链公司,车厂只负责其中最关键的开发设计,车身、发动机等部件的打造,以及最后的总装过程。而同时供应链公司则可以吸纳多家车厂的需求,通过规模效应进一步降低单个产品的制造成本。
现实中,汽车工业也的确是这样做的。
整体的合作框架有了,接下来则是更多需要解决的问题,对于高端市场来说首先要面对的就是“品质”问题。虽然实际上部件是由供应商生产的,但消费者只会看到车厂的品牌。想要解决这个问题,办法只有一个——车厂帮助供应商,在技术和经验上实现足够的积累。
华晨宝马也是这样做的,不仅在名华模塑生产3系前保险杠遇到问题时,帮他们向国外同行请教,之后也以同样的方式,让名华模塑帮了南非同行一把。
剩下极少数部件,如整辆车数字系统沟通所依赖的主线束产品,华晨宝马则选择了纯德国外资的德科斯米尔来合作。要知道在这一类的产品上,宝马集团和德科斯米尔的合作最早甚至可以追溯到1966年。
结果很明显,这些供应链公司在自身不断成长的同时,也反过来保证了车厂自己的产品质量。同时,这些供应链公司在跟车厂、外国同行的交流,在具体制造流程的不断熟悉、打磨中,还创新出了一系列全新的操作方式,很多还已经成为了专利。
从名华模塑生产三系前保险杠为例,因其材质不同于车身,采用增强增韧改性聚丙烯,为保证颜色、外观与金属车身一致性,名华定期和华晨宝马车身核对颜色控制数据,同时为保证油漆与塑料材料的附着力满足宝马的全球标准要求,在喷涂前使用1200℃火焰对保险杠进行表面火焰处理,提高材料表面活性。
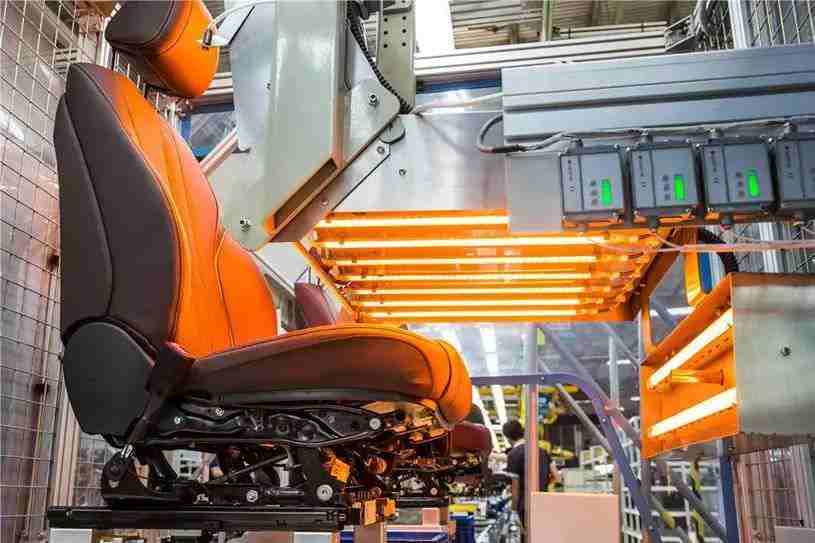
金杯安道拓生产的5系座椅
又比如金杯安道拓生产的5系车座椅,其皮质表层在经历切割、缝制、填充等一系列操作之后,还要用3道工序对座椅加热来消除可能存在的折痕和皱褶,并且在多道人工检查合格之后才可下线。
这一系列优质而又配合紧密的供应链,是15年不间断“培养”和“优化”的结果。
正如华晨宝马总裁兼首席执行官魏岚德博士自己所说:“绝大部分跟我们一起成长起来的供应商都是非常感谢我们的。因为技术和产品质量的高要求,以及持续不断施加的压力,让他们能不断的获得世界上最先进的技术,提高他的产品质量,从而最终也提高我们的产品质量,其实对他长远的发展是非常好的,也是今天我们供应商能够成功成长为国际化独角兽企业的关键。”
工业4.0时代的挑战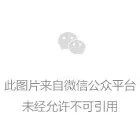
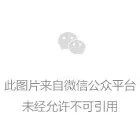

华晨宝马新大东工厂工业4.0应用:激光扫描
一边是来自世界工业最强德国的老牌车厂,一边是中国制造业的传统重镇沈阳,这本身就是一次难得的最先进工业制造技术学习机会。这一点曾在参观中多次体现。
但在整体汽车制造业不断升级的趋势下,制造技术和理念的升级,与其说是机遇,不如说是“挑战”。
首当其冲的就是全系统的定制生产能力,作为现代汽车业的一大特点,越来越多的个性化、可定制选项,一直是个必须克服的“麻烦”。
而华晨宝马选择的方案是“一张大网”:利用网络将车厂和一众供应商连接起来,在用户完成个性化定制下单之后,将订单的需求再分解成具体供应商专门负责的部件。最后再将这些部件运到总装车间,将他们变成可以售卖的汽车。

华晨宝马新大东工厂工业4.0应用:无座座椅
这个过程中的厉害之处在于:生产环节都是围绕订单进行的,很多供应商的零部件制造、组装,只比最后的装配快4小时,供应商手头的存货甚至仅够华晨宝马使用半天,库存率低得惊人。
在数量庞大的订单和复杂的供应链体系下,不出错则是另外一个难题。解决办法是给每个部件配上一个“身份”——二维码。每一道工序开始之前,工人都要扫一次那个二维码,工作站的屏幕上就会出现这台车目前工序下需要做的操作、以及各式零配件的参数,基本不可能犯错。
同样也是因为二维码的存在,也让物料的流转变得极度流畅。例如一辆经过定制的半成品3系轿车,在被运送到特定工序之前,系统就会知道这道工序需要的零部件在哪里,然后工厂内的物流小火车就会稍稍提早,将零部件运送到流水线旁边。
对错误的监控、预防、统计、修正算是“工业4.0”另外一方面的体现。
在名华模塑参观过程中,他们用一连串的大型注塑机以及KUKA机器人来组成流水线,这条流水线的责任是制作一种将气囊嵌入的车内塑料面板。在整个部件生产流程完成之后,机器手会拿起部件,在数个摄像头面前,多次旋转、移动,直接利用人工智能驱动的图像识别来判别是否属于良品。

沈阳名华模塑的工人正在质检
而在打造3系车尾保险杠的过程中,需要用肉眼检查是否有划痕,但最终记录的并不只是“有无划痕”,而是质检员直接在工作站中点出来划痕在产品中出现的位置。在划痕多次出现在同一个区域的时候,就可以反过来检查,究竟是生产流程中的哪一个环节导致了这些划痕。
这些最领先的制造业生产理念,就这样在日常的合作中,渗透到了中国供应链企业的管理和运行当中。进而减小了制造业升级可能带来的冲击。
布局未来,和造车真正的“难”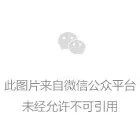
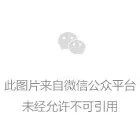
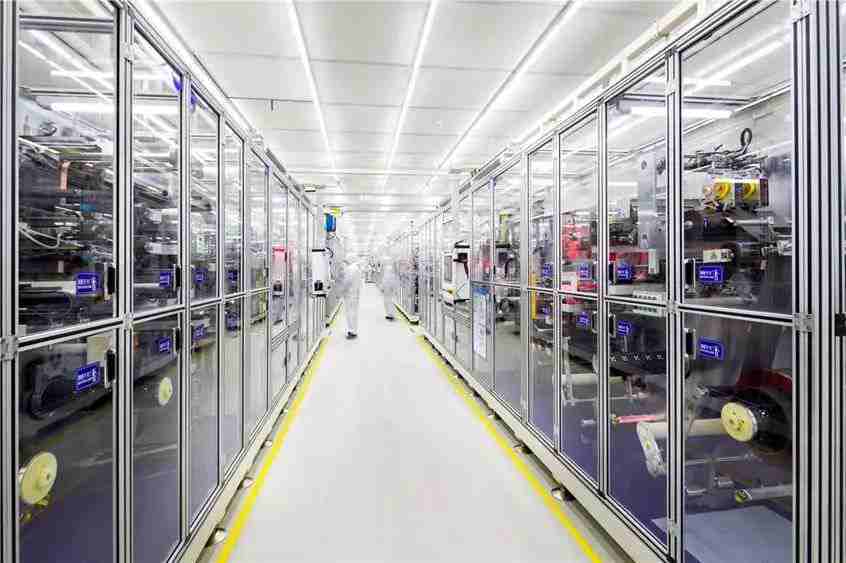
宁德时代电芯生产车间
不管品牌有多么响亮,也不管目前传统车辆卖的有多好,对于新能源车的布局,都是车厂当下必须做的一件事。
在这一点上,华晨宝马已经走出了相当远的距离。今年7月,继宁德时代和宝马集团确立了价值40亿欧元的电芯采购意向后,华晨宝马也和宁德时代签订了一系列深化战略合作的协议,其中就包括了购买位于福建宁德的一项电池产能建设项目,以便项目落成之后,能够专门为华晨宝马服务。
据了解,双方的合作早而有之,尤其是在部分高精尖的加工技术上。华晨宝马甚至直接派出工程师,和宁德时代一起,建立了第一条电池单元模块组装生产线,这条“标准生产线”也被宁德时代直接作为拓展参照的原型并在随后不断升级。
可以预见,2020年将在沈阳投产的纯电动汽车BMW iX3,肯定是不用愁电芯了,大概率会成为华晨宝马自己的又一个里程碑。
对于华晨宝马这些年来在供应链上面的努力,魏岚德博士在采访中是这样解释的:“我们的战略非常简单也非常明确,最核心的就是要做世界上最好的整车厂,要生产世界上最高质量的产品,其前提是要求我们的供应商能够为我们提供世界上最优秀、最高质量的零部件。”
“因为归根到底,我们需要对消费者负责”他随后又补充了一句。
这或许也是为什么华晨宝马15年来,坚持走这样一条“更难”的路线的原因。一点点不断升级自己的实力、提升供应链的整体水平、提早未来布局。
一方面是因为汽车这样一个特别重视安全、特别重视细节、特别需要时间打磨产品的行业,将发展速度放在所有指标之前,这本就是本末倒置。
其次是制造业并没有那么多“弯道超车”的机会,很多核心的硬实力都需要长期努力才能形成。一味求快,无异于给自己埋雷,假如产品后续出现问题,那真的得不偿失。
从另外一个角度来看,15岁的华晨宝马也给了我们一个宝贵启发:造车真正难的,是要坚持一个“单纯又直接”的动机。

特别策划
最新评论
推荐文章
作者最新文章
你可能感兴趣的文章
Copyright Disclaimer: The copyright of contents (including texts, images, videos and audios) posted above belong to the User who shared or the third-party website which the User shared from. If you found your copyright have been infringed, please send a DMCA takedown notice to [email protected]. For more detail of the source, please click on the button "Read Original Post" below. For other communications, please send to [email protected].
版权声明:以上内容为用户推荐收藏至CareerEngine平台,其内容(含文字、图片、视频、音频等)及知识版权均属用户或用户转发自的第三方网站,如涉嫌侵权,请通知[email protected]进行信息删除。如需查看信息来源,请点击“查看原文”。如需洽谈其它事宜,请联系[email protected]。
版权声明:以上内容为用户推荐收藏至CareerEngine平台,其内容(含文字、图片、视频、音频等)及知识版权均属用户或用户转发自的第三方网站,如涉嫌侵权,请通知[email protected]进行信息删除。如需查看信息来源,请点击“查看原文”。如需洽谈其它事宜,请联系[email protected]。