PdM--赴美办企业须考虑的检修方式
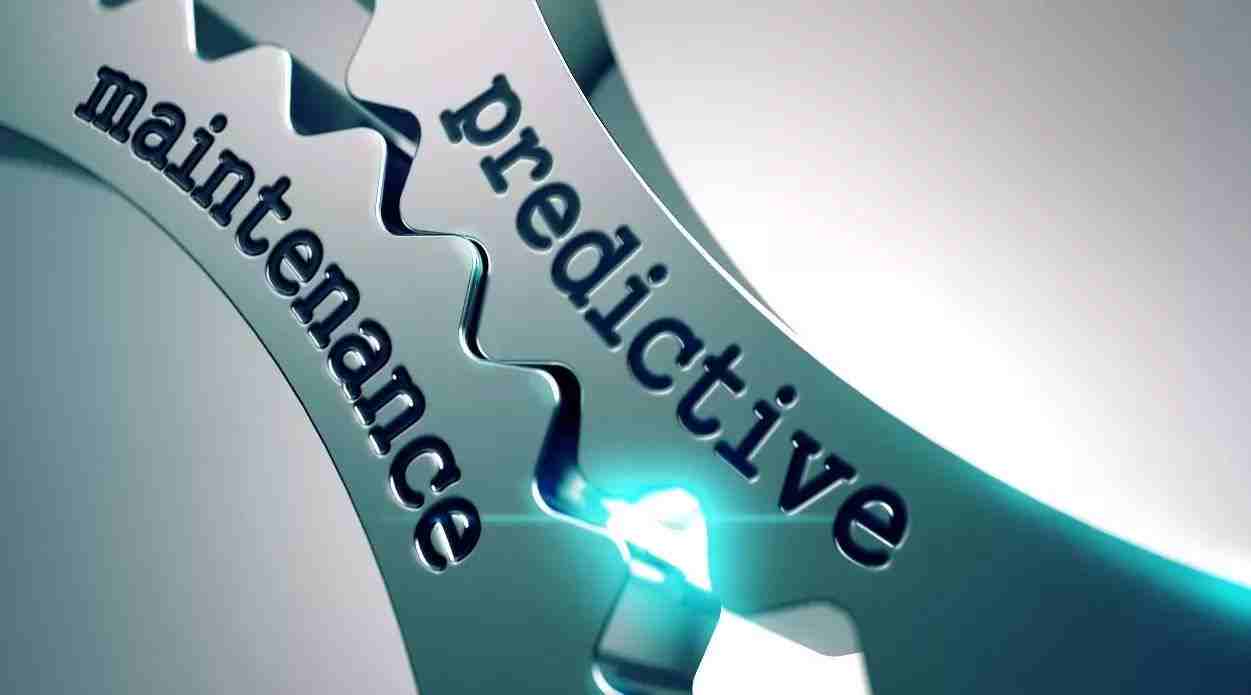
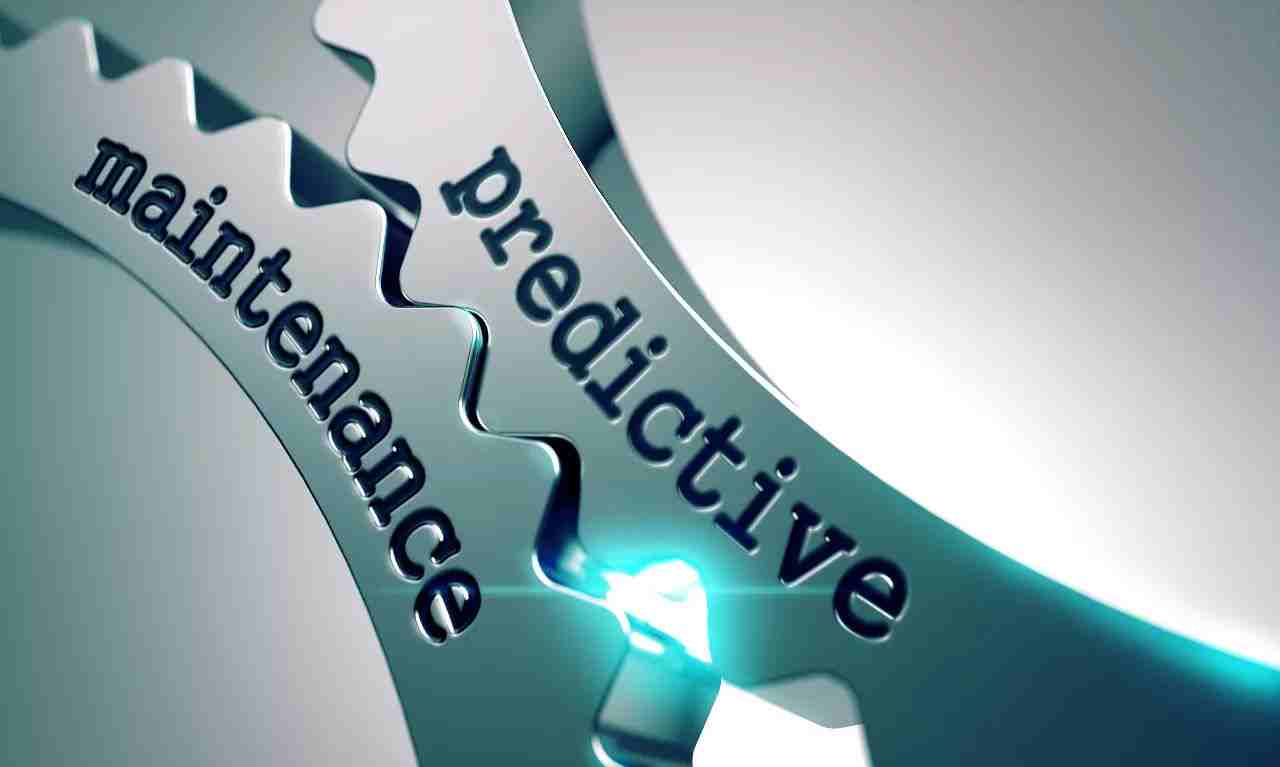
赴美投资建厂,面对的最大差异可以归结为两点,
一是自动化。
劳动力成本高导致所有思路基于省人工不省设备材料。省人工的投资,一般都比较划算。
二是标准化。
教育程度高的劳动力成本更高,所以标准化、模块化可以让工作尽可能降低对工人的技能要求。
三是提前期。
劳动力成本高,就是时间成本高,所有事情都要提前预约、提前安排。任何赶工导致的加班加点,所需要的劳工成本更更高。
今天来说一说跟这三者都息息相关的一样工作 -- 设备维护。
我们不应该轻视设备维护维修。未来工厂自动化程度越来越高,生产操作变得越来越简单的同时,机械设备维护的要求其实会变得越来越高。
一方面是各种电器元件和零配件的种类越来越多;
另一方面,设备停转的机会成本会变得更加巨大。
随着人力成本高企和自动化程度提高,如何增加设备运行时间,提高设备效率,将会是中国制造业未来面临的核心问题。
而对于赴美投资建厂的中国企业来说,设备维护便是一种眼下立马就要面对的挑战。
任何设备都是会坏的,所有高速运转的部件都会磨损,磨损了就需要购买更换新的零配件。
而中美企业运营的一个巨大差异就是采购周期。
在供应链完善、物流快捷的中国,如果机器坏了,或许只要一个电话,就有供应商可以加班加点,当天送到。
而在美国,很多零件已经不在本土加工,需要从世界各地采购的,经销商的仓库也只建在全国几个大的枢纽站,任何配送常常是需要好几天,甚至一些大型部件需要通过海路进口,需要几周几个月。
美国人习惯了慢条斯理,做生意也看自己日程安排,如果办理加急,就意味着让大家随着你的需要,来改变早就定好的日程。任何的加急,不是不可以,但额外的费用常常非常惊人。
所以最保险的办法就是预先采购配件,以防万一。
但要采购多少呢?
理论上讲,每个零件都可能会坏掉的。
再买一条生产线,给其他生产线拆作备用件么?
设备供应商通常会给出一个推荐的采购清单,但往往非常保守,占用资金非常庞大。
在这样的环境下,PdM- predictive maintenance 就显得非常有用。
说PdM之前,先提一下在中美都很普及的
PM(preventive maintenance)这两种方式最主要区别是,
PM就是定期的,预防性;而PdM是预测性的。
无论美国,还是中国,等到机器坏了再修,都是最被动的选择。
例如汽车的定期保养就是一种PM。
你换机油的时候,并不是汽车真的已经坏了,而是汽车厂商根据他们的数据和经验,推荐六个月作为一个比较合理的换机油间隔。
但因为每个司机操作习惯和汽车实际运行情况各不相同,这种基于固定时间的PM会有浪费或者不及时的可能。
机器设备也一样,所有高速旋转的部件都会有轴承以及润滑,很多齿轮传动的地方也需要冷却和润滑。这些都可以通过定期检测和更换来保证设备的运行安全。但这样的保养,要么换的过早造成浪费,要么不能及时的发现早已存在的问题。
所以在六十年代,衍生出了PdM--predictive maintenance,一种更主动的维修手段。
目前我接触过的方式有:
1.对润滑油料取样,送检分析,来推测设备的磨损情况。
2.分析核心运转部件的振动和噪声异常。
3 红外线感测成像来检测设备的温度异常。
4 超声波探测潜在渗漏裂缝
用到的仪器:
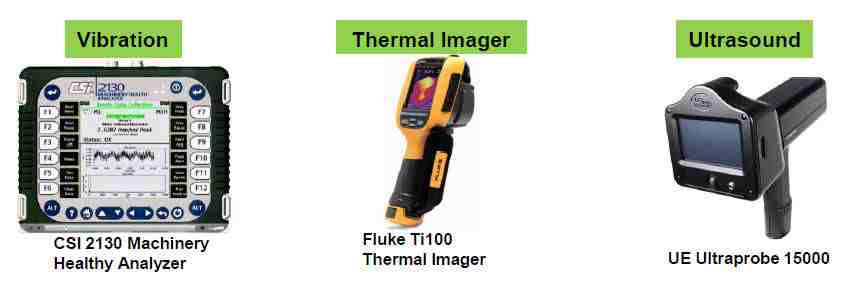
主要思想就是通过各种仪器传感器收集运行数据,加以分析,提前预测到未来可能损坏的部件(轴承、皮带、齿轮等等)以及需要更换的油料等,从而可以提前安排检修人员,合并检修任务,及时采购零配件等等,以达到节约劳工成本,降低零配件库存,延长设备运行时间。
相信这一理念,在未来的无人工厂,会越来越普及。
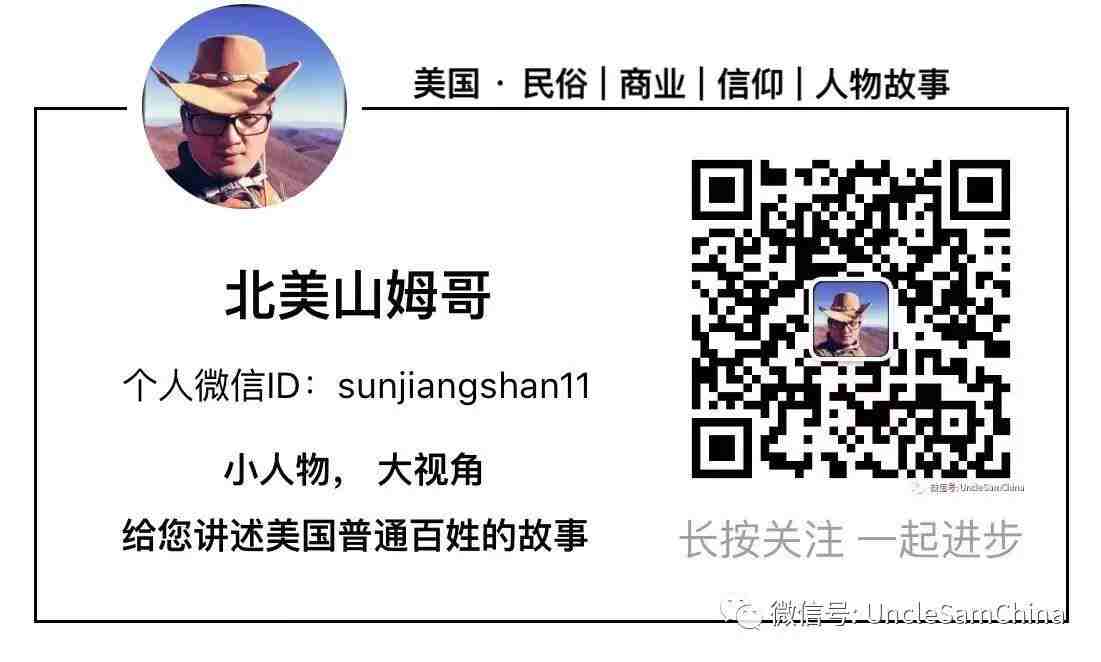
最新评论
推荐文章
作者最新文章
你可能感兴趣的文章
Copyright Disclaimer: The copyright of contents (including texts, images, videos and audios) posted above belong to the User who shared or the third-party website which the User shared from. If you found your copyright have been infringed, please send a DMCA takedown notice to [email protected]. For more detail of the source, please click on the button "Read Original Post" below. For other communications, please send to [email protected].
版权声明:以上内容为用户推荐收藏至CareerEngine平台,其内容(含文字、图片、视频、音频等)及知识版权均属用户或用户转发自的第三方网站,如涉嫌侵权,请通知[email protected]进行信息删除。如需查看信息来源,请点击“查看原文”。如需洽谈其它事宜,请联系[email protected]。
版权声明:以上内容为用户推荐收藏至CareerEngine平台,其内容(含文字、图片、视频、音频等)及知识版权均属用户或用户转发自的第三方网站,如涉嫌侵权,请通知[email protected]进行信息删除。如需查看信息来源,请点击“查看原文”。如需洽谈其它事宜,请联系[email protected]。